Quality
A PRODUCT TESTED IN EVERY PHASE
Quality Control Laboratory
Our Quality Control Laboratory continuously monitors and inspects every stage of the stainless steel tube production process.
It consists of a team of highly skilled technicians, regularly trained and equipped with advanced testing devices that operate 24/7 to ensure the compliance of processed products.
The goal is to provide customers with reliable products that meet their specific requirements.
Quality policies
CSM TUBE's Quality Policies focus on the following areas:
-
Excellence in production
-
Effectiveness, efficiency, and data analysis
-
Personnel growth
-
Customer-centric approach
-
Optimization of production processes
-
Continual Improvement of the Quality Management System
Quality, safety and environment
We guarantee high-quality standards and compliance with international regulations for our customers, supported by our certifications.
Non-destructive Tests
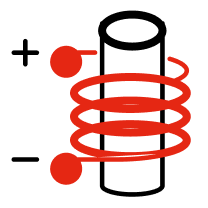
Eddy Current Testing / EN ISO 10893 Part 1 & 2
Continuous inspection using the Eddy Current technique according to EN ISO 10893: Part 1: Ensures hydraulic integrity. Part 2: Detects defects and imperfections.
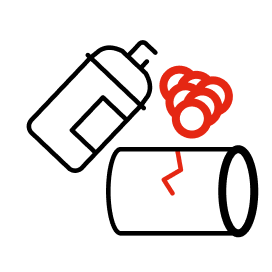
Liquid Penetrant Testing
In accordance with EN ISO 10893-4/ASTM E165, surface integrity is inspected for defects in metallic materials through the application and removal of a colored liquid.
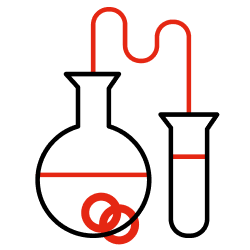
Chemical Analysis / PMI XRF Inspection
Chemical analysis using XRF Spectrophotometry (X-Ray Fluorescence) is conducted to inspect raw materials and and reduce risk. Results are automatically verified by the company's operating system.
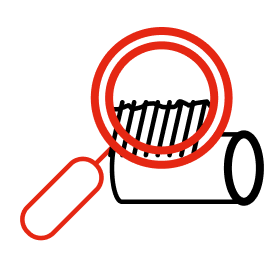
Roughness Measurement EN ISO 4287
Surface roughness and 3D surface reconstruction analyses are performed using advanced 3D optical microscopy.
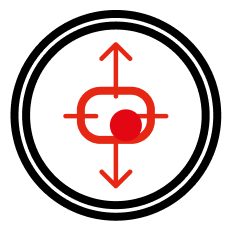
Dimensional Inspections EN ISO 1127
All production equipment is equipped with calibrated measuring tools to continuously measure the diameter and length of products. Results are saved in the company's operating system.
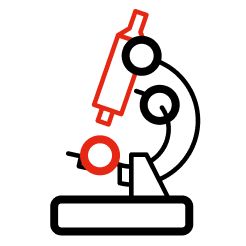
Micrographic and Macroscopic Analyses
Grain size, base material structure, and welded joint analyses are periodically conducted during production to verify the structural conformity of finished products.
Destructive Tests
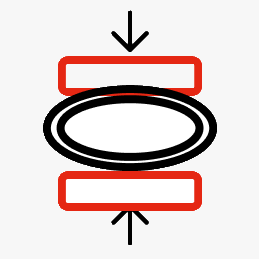
Flattening Test / EN ISO 8492
Flattening tests, with welds positioned at 90°, are conducted according to EN ISO 8492. These tests are performed inline periodically as per the control plan, with results recorded in the company’s operating system.
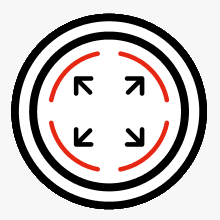
Expansion Test
An end ring from a tube is expanded using a conical mandrel until failure occurs. This evaluates the tube’s ability to undergo plastic deformation and identifies potential manufacturing defects.
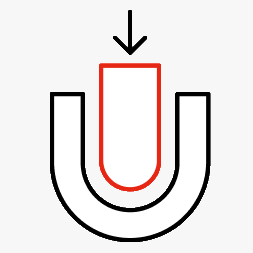
Reverse Bend Test / EN ISO 5173
Reverse bend tests are performed on weld seams to ensure joint compliance after deformation. Results are recorded in the company’s operating system.
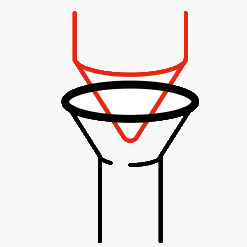
Drift-Expanding Test / EN ISO 8493
Mandrel expansion tests verify the joint’s compliance after conical mandrel expansion. These periodic inline tests follow the control plan, with results saved in the company’s operating system.
Mechanical Tests
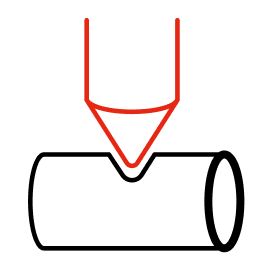
Hardness Test
Surface hardness is tested using standard measurement techniques (typically Vickers and Brinell), with portable durometers in production areas and bench durometers in laboratories. Tests are conducted periodically, and results are recorded in the company’s operating system.
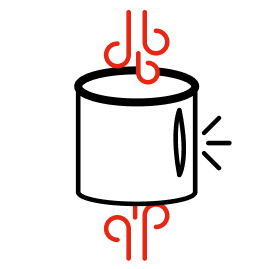
Bursting Test
Bursting tests determine: the maximum diameter reached by the sample after explosion, the maximum pressure before the explosion.Testing equipment can reach up to 1,000 bar of internal pressure, with periodic tests performed inline according to the control plan. Results are saved in the company’s operating system.
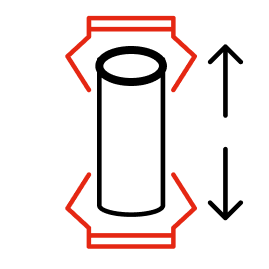
Tensile Test / EN ISO 6893 – 1
Tensile testing evaluates the mechanical properties of heat-treated tubes. The dynamometer automatically uploads test results to the company’s operating system and inline PCs. Tests are conducted periodically per the control plan.
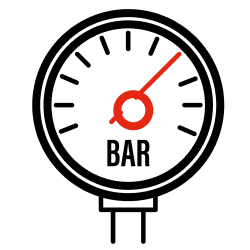
Underwater pressure test
Pressure tests are conducted in water to ensure weld seam integrity for 100% of the coils produced. The test can be performed at a maximum internal pressure of 100 bar. Results are recorded in the company’s operating system.
All quality control tests on products and processes are performed on samples identified via marking. At any time, results can be traced and verified through a digitalized system that integrates data collected by operators, production lines, and laboratory instruments.